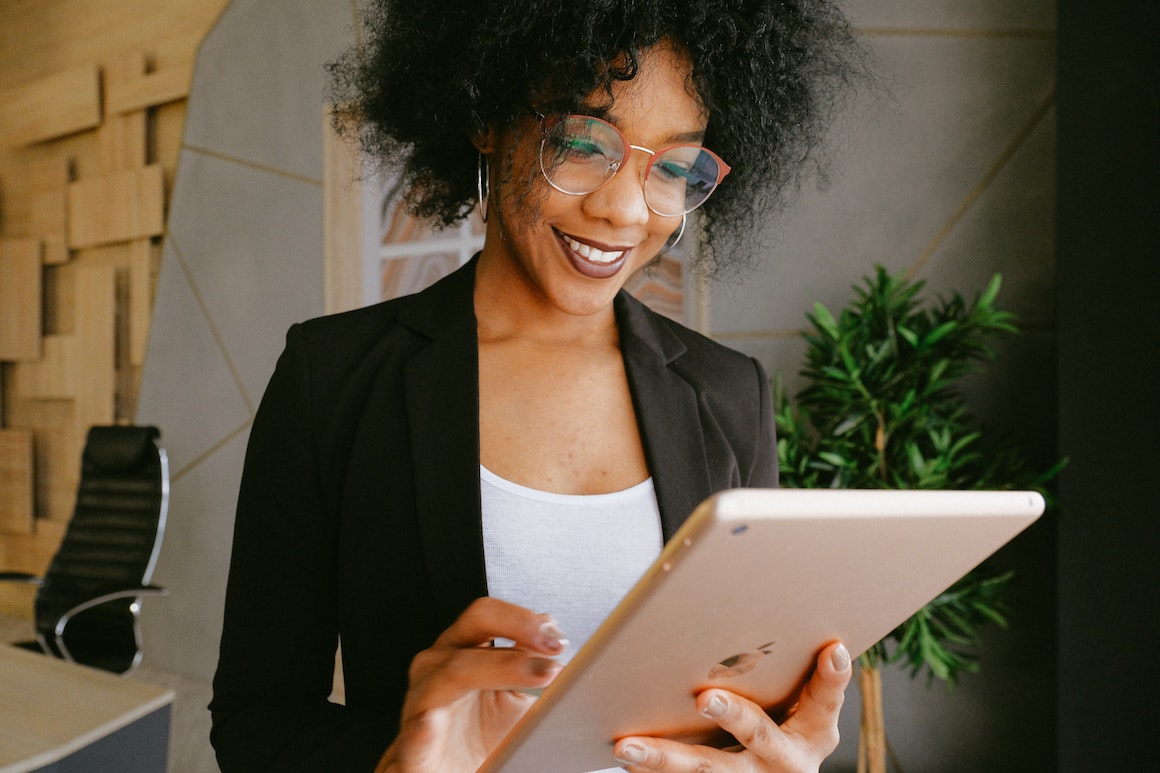
6-minute read
When asked whether they’re doing enough to minimize risk and protect employees, most employers
would probably answer ‘yes’. While it is unrealistic to assume that every company is making the
utmost effort with regards to safety management, it is easy to see why they might think they are.
Factors such as reasonable expenditures on safety and insurance, or a lack of major safety incidents,
might paint a picture of a relatively low-risk workplace.
The truth is often murkier. There are many different approaches to occupational health and safety,
and priorities and features vary by company and industry. However, the most successful programs
often have one thing in common: an integrated safety management system. This kind of system
helps to not only put safety standards into practice but also to evaluate and reduce many risks of
doing business, from high insurance costs to compliance issues and fines. Here’s why a safety
management system is a key to reducing risk, managing cost, and promoting a dynamic safety
culture for all.
Reason 1 – The Systems Approach
First of all, what makes a safety management system so effective at managing risk? It’s all about
integration. A systems-based approach to workplace safety connects all relevant organizational
departments in service of safety. While a safety management system is primarily concerned with
occupational health and safety, it succeeds by integrating other branches of the organization into
this process.
How does this work in practice? For instance, financial risk analysts can communicate with the
managers who oversee the safety hazards that impact those financial risks. These departments can
share strategies and synchronize their individual approaches to the problem, rather than working at
odds with each other. A systems approach to workplace safety recruits all relevant parts of an
organization to achieve the organization’s occupational health and safety goals.
This coordinated effort means that a safety management system helps offset many different types
of risks. It improves tracking of relevant safety data, including training and documentation, and this
contributes to informed decision-making. It also encourages a proactive, rather than reactive
approach to safety, which ultimately improves resource allocation and reduces costs.
Reason 2 – Beyond Compliance
Monitoring compliance is an indispensable feature of most occupational health and safety programs.
However, relying on compliance alone is both ineffective and incredibly risky in the long run.
Regulations can be very slow to change, which means they do not always perfectly correspond to
conditions on the ground. Even if an organization rigorously follows compliance standards, incidents
or injuries can still occur. According to safety expert and consultant Pam Walaski, compliance is only
the starting point for a strong safety management system. The end goal is to build upon compliance
standards with specific and relevant metrics that ensure worker safety. This approach goes hand-in-hand with the most recent OSHA guidelines for occupational health and safety programs, which
emphasize preventive rather than reactive behaviors.
For example, when an incident occurs, employers must file a report describing details and causes.
This step ensures that employers are compliant with incident-reporting regulations. However, as
many safety professionals know, safety-related incidents do not happen in a vacuum. In other
words, there is often more to an incident than the isolated details of the case. An organization with a
strong safety management system will go beyond compliance requirements to identify the
conditions and precursors that led to the incident in the first place. Walaski notes that common
precursors, such as non-routine work or the presence of contractors, can open the door for
preventive interventions into potentially risky situations.
A systematic approach uses compliance only as the baseline while asking deeper questions and
identifying patterns that lead to poor safety outcomes. An organization that fails to identify and
address the conditions and precursors that lead to occupational hazards is at serious risk of
re-occurring safety incidents.
Reason 3 – Cost Reduction
One of the common costs of doing business in any industry is insuring employees against injury and illness sustained on the job. Determining premiums for workers’ compensation insurance has a lot to do with a company’s safety culture and safety record. On the one hand, poor risk assessment leads to employers spending an inadequate or inaccurate amount on insurance, leaving employees unprotected and employers vulnerable to lawsuits. In addition, poor evaluation and follow-up on safety incidents diminish a company’s safety record, leading to higher insurance premiums.
A safety management system addresses these discrepancies by integrating cost reduction and risk
assessment. This approach emphasizes prevention and safe practices, ensuring that employees are
protected from harm and fully covered in the event of an incident. On the employer’s side, improved
risk assessment means that insurance premiums correspond to the company’s safety record.
Reason 4 – Basic Maintenance
There is nothing more disruptive to productivity than a sudden interruption due to faulty equipment
or a hazardous spill, as such events can also affect all other productive activities. Fortunately, a
safety management system can keep track of even these most basic occurrences and their
resolution.
How does this happen? Because so many safety incidents are the result of human decision-making
or error, addressing the problem requires minimizing these risks. An integrated safety management
system creates processes that reduce the likelihood of human error or improvisation. For example, if
there is a spill, workers should not have to wonder how to properly handle or dispose of toxic
materials and waste.
Maintaining a safe and clean working environment makes random inspections or audits a lot easier
to deal with. Needless to say, diligence in this area also has a financial payoff, preventing the
increases in insurance premiums that result from unsafe practices. Without a safety management
system, a company is at tremendous risk from the safety and financial consequences of equipment
failure, mishandling of hazardous waste, and improper safety procedures.
Reason 5 – Documentation
Recordkeeping is an instrumental part of a strong safety culture, but it is also one of the more
tedious tasks of occupational health and safety work. Poor or inconsistent recordkeeping poses a
major risk to an organization. Without a recorded history of safety incidents and responses, it is
much more difficult to prove that a company took proper safety precautions and implemented
corrective action in response to incidents.
A safety management system provides documentation of individual incidents, as well as a pattern of
safety practices. This information can be readily accessible if needed on short notice, and it can
provide critical evidence in the event of a lawsuit. While good safety practices should reduce the
likelihood of lawsuits in the first place, a ‘paper trail’ can bolster the company’s case by providing a
track record of good safety practices.
Reason 6 – Training
Without a doubt, employees who are either improperly trained or not up-to-date in their training
can pose a serious risk to their organization. Lapses in employee training are especially concerning in
industries that are high-risk or subject to frequent regulatory updates. Training often suffers due to
the sheer logistics of monitoring training for hundreds or thousands of employees, each of whom are
at a different stage of employment or have different training needs. Unfortunately, pieces of training
are not always current or relevant or are delivered in a classroom setting that is disconnected from
the hands-on work that employees perform every day.
OSHA training violations can carry a fine of over $13,000, so it is easy to see why failure to properly
train employees presents a major financial risk.
How does a safety management system tackle these training challenges? The most effective
systems can assign pieces of training to relevant employees, track completion, and monitor retraining or supplementary training schedules. An integrated safety management system also helps facilitate hands-on training that goes beyond the classroom. In this context, employees are taught how to recognize and respond to risks that occur on the job. This approach empowers employees to
perform risk evaluation every day, on their own and gives them the tools to respond to and minimize
risk. All these different elements of training can be used to document the overall job preparedness
of employees, another factor that ultimately helps lower insurance costs.
Reason 7 – Integrated Risk Management
Having separate, standalone safety standards or departments can pose serious risks for an
organization’s occupational health and safety efforts, while also handicapping the prevention of, and
response to, safety incidents. One of the hallmarks of a safety management system is that risk
management is a core component of the system’s design, rather than a separate external variable.
When risk management is woven into workplace safety, there is a higher likelihood of successfully
evaluating and addressing safety risks. This means identifying not just the causes, but the conditions
and precursors that give rise to incidents, illness, and injury.
A safety management system also promotes strategic communication between different areas of the
organization. The sharing of risk evaluation data contributes to a more coordinated and holistic
approach to safety management. A safety management system recognizes the importance of
compliance while also stressing continuous risk evaluation and internal accountability as equally
important elements of occupational health and safety. Integrating the entire OHS infrastructure
bridges the gap between external standards, and local metrics reduce risk and promote a strong
safety culture.
Click here to find out more and arrange a free demonstration
Share: