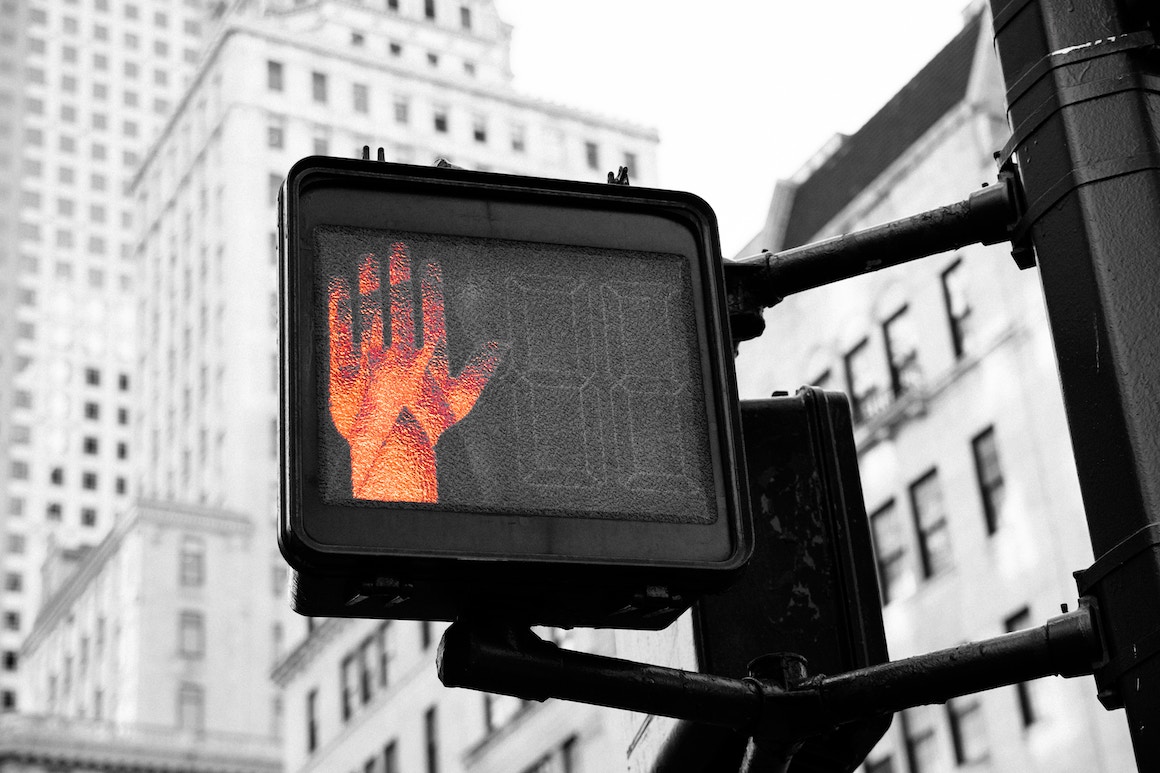
What makes a health and safety system truly successful? Good question.
Knowing the rules and following them is one piece of the puzzle: Think recordkeeping, incident
tracking, and regulatory compliance. Just as important, though, is avoiding major safety mistakes.
Although this sounds obvious, some of the biggest workplace safety mistakes can be difficult to
recognize and prevent.
When thinking about safety mistakes, those which come to mind are usually dangerous accidents or
exposure to hazards. However, the following five problem areas may not be at the top of the list
right now, but they sure should be. Here’s why, and what you can do to prevent them.
Safety Mistake #1: Inadequate or rushed training
It makes sense that employers would want to onboard new employees as efficiently as possible.
From a financial standpoint, hiring and training is a costly process. The more efficient the training,
the sooner the employee can become a productive contributor to the company. While expedited
training might seem appealing, taking the time to train and onboard properly can have numerous
health and safety benefits.
In matters of workplace health and safety, detailed and thorough training can set a strong standard
and example from an employee’s very first day on the job. Not only does it help arm employees with
the know-how to prevent workplace safety mistakes, but it also communicates that safety is a
priority.
Although employees and employers commonly agree that training is important, most people don’t
enjoy sitting through lengthy training sessions, whether in a classroom or in front of a computer.
This can harm the quantity and quality of information that employees absorb. A strong health and
safety system makes the best use of employee time and attention by delivering training that is
timely, hands-on, and relevant. EHS management software can help provide more accessible and
convenient training, allowing employees to complete it at their own pace or within a certain
timeframe. It also tracks employee progress and stores training documents for easy retrieval.
Safety Mistake #2: Missing near-misses
A near-miss incident can feel a relief, and it is easy to move on and forget what happened once the
threat has passed. However, neglecting to follow up on a near-miss is a major risk factor, because it
increases the chances that the issue will reoccur. How do you ensure that a near-miss doesn’t
snowball into a serious incident?
Near-miss reporting requires clear and seamless communication throughout the organization. When
employees and management are not sure whether or how to report near-misses, it affects not just
that single case, but the overall quality of incident reporting data.
Over time, proper near-miss reporting results in a trove of accurate and potentially life-saving data.
To achieve this level of reporting, it’s important to communicate a clear, straightforward policy on
the reporting process. One of the first and simplest steps is to define exactly what is meant by a
near-miss. For example, The National Safety Council defines a near miss as “an unplanned event that
did not result in injury, illness, or damage – but had the potential to do so”. The definition can be
tailored to make it relevant to the organization and the industry, and it should be made known to all
personnel involved in safety reporting.
Most importantly, regular discussion of near-misses normalizes reporting and creates a clear line of
communication between workers and management. For example, asking about near-misses in daily
meetings or through reporting dashboards can turn attention to recurring issues that need to be
addressed. The organization should establish a clear chain of command and protocol for addressing
near-misses, including reporting, analysis, prioritization, and solution.
Safety Mistake #3: Missing Regular Maintenance and Inspection
Equipment maintenance is extremely important, but doesn’t it always seem to come up at the most
inconvenient time? If maintenance and upkeep are done on the spur of the moment, it’s easy to
think of all of the reasons why the equipment is needed and cannot be turned off, even briefly.
Putting it off or adding ‘equipment maintenance’ to the mental to-do list might make us feel better
in the moment. Unfortunately, the delay only increases the chances of a completely preventable
equipment failure and poses a major safety hazard to employees.
The solution is regularly scheduled maintenance checks, built into workplace health and safety
software, like Donesafe. This can help address one of the biggest reasons for putting off
maintenance – loss of productivity. Scheduling maintenance regularly can help prepare and account
for a temporary dip in productivity. The alternative, doing maintenance only when the equipment
malfunctions, is a surefire way of losing productivity. Planning maintenance ahead of time—and
abiding by that plan—helps accommodate any downtime resulting from the inspection. Regular
maintenance is also crucial for preventing safety incidents resulting from faulty equipment.
Safety Mistake #4: Failing to use proper tools and protective equipment
Improvisation and creative thinking are valuable skills in any workplace. In the interest of time and
efficiency, a worker might choose to improvise or use the available tools to complete a task,
especially if that task is urgent. Unfortunately, taking shortcuts to get the job done can result in
entirely preventable workplace safety mistakes. Substituting an imperfect tool for the correct tool
might get the job done, but it’s also likely to increase the risk of injury. Likewise, completing a task
‘on the fly’ might mean that proper safety equipment, such as hard hats or reflective clothing, is
inaccessible.
Avoiding this issue is a matter of preparation as well as communication. Employees should have the
right tools to do their job, and they should be instructed on the proper handling of these tools. The
issue also needs to be addressed through teamwork-centered communication. Why? Because, for
instance, a fall from an improperly placed ladder will injure both the person on the ladder and those
beneath it. Misusing equipment and failing to protect oneself pose risks not just to the individual,
but anyone working alongside them. Team-oriented communication promotes a shared
responsibility towards oneself and others. Workers who engage in risky behavior may change that
behavior if they realize that their actions endanger others as well as themselves.
Safety Mistake #5: Failing to prioritize your health and safety system
A robust health and safety system is made up of so many moving parts: incident reporting,
standards, hazard management, regulatory compliance, and training, just to name a few. Many of
these areas are subject to continuous updates and changes and require ongoing monitoring and
maintenance. Luckily, these tasks can be managed in the one place by investing in comprehensive
health and safety management software. Choosing to bring the entire health and safety system
under a single umbrella also sends a clear message that ‘health and safety’ is more than just a slogan
– it’s an organizational priority.
“Health and Safety” is more than just a slogan, but rather an organizational priority
How can health and safety software help prevent these and other common safety mistakes? First, it
simplifies training and makes it more accessible and convenient for employees to complete. It
provides a database for tracking and following up on near-misses, and reminders to complete
regular equipment maintenance and inspection. Health and safety software, like Donesafe,
automates the busy workload of health and safety management, allowing more time for important
hands-on safety practice and face-to-face interactions.
Contact us today to find out how Donesafe the #1 all-in-one EHS platform can help
Share: